What are process key figures?
Process indicators - also known as key performance indicators (KPIs) - are central metrics for evaluating business processes. They enable a quantitative analysis of the effectiveness, efficiency and quality of processes in companies. Process KPIs are used to objectively assess process results and form the basis for data-based decisions in process management.
Importance of Process Key Performance Indicators
Process KPIs in a company provide essential insights into the performance of operational processes. They help to identify bottlenecks, weak points and inefficiencies. Targeted evaluation allows measures for process optimization to be derived and performance to be increased. They also enable benchmarking with other companies or industry standards and promote continuous improvement through systematic monitoring and control.
Types of Process Key Performance Indicators
Process KPIs can be divided into several categories, depending on the focus of the process analysis:
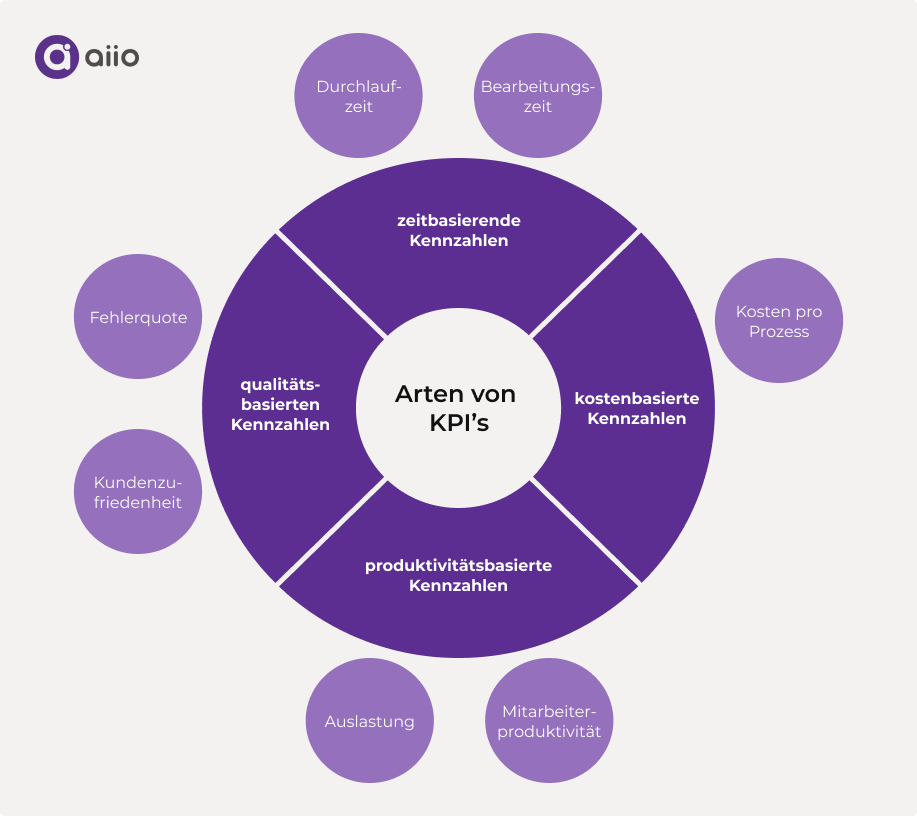
1. time-based process indicators
- Throughput time: Measures the entire time span of a process from start to finish. Short throughput times stand for fast and efficient processes.
- Processing time: records the time for individual tasks within a process. Low processing times reduce waiting times and improve overall performance.
2. quality-based process indicators
- Error rate: Indicates the number of process errors. A low error rate indicates stable, low-error processes and increases customer satisfaction.
- Customer satisfaction: Measures customer satisfaction with the service provided. It is a key indicator of process quality and service success.
3. cost-based process indicators
- Costs per process: Includes all direct and indirect costs associated with a process (e.g. personnel, materials, energy). This key figure helps to identify potential savings and control process costs.
4. productivity-based process indicators
- Utilization: Shows the relationship between actual and potential performance. High utilization means efficient use of resources.
- Employee productivity: Evaluates how efficiently employees participate in processes. This key figure helps to realize optimizations in personnel management.
Examples and application areas
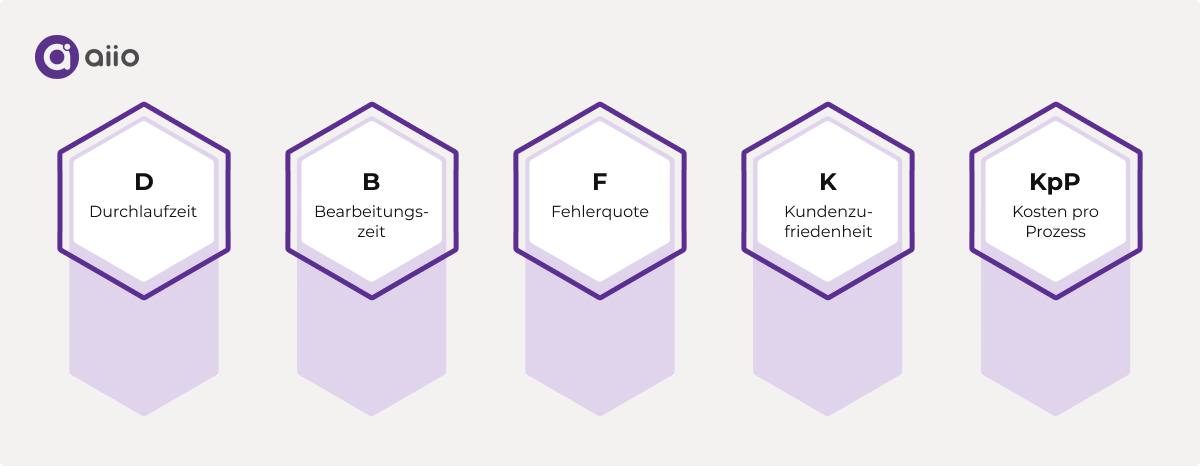
Some typical examples of process indicators in practice:
- Reduce lead time to enable faster order processing
- Analyze processing times to streamline internal processes
- Measure error rate to improve process quality
- Record customer satisfaction in order to systematically turn feedback into improvements
- Calculate costs per process to create cost transparency and make economic decisions
Depending on the industry, other key figures such as reject rate, waiting time or employee satisfaction can also be used.
Conclusion
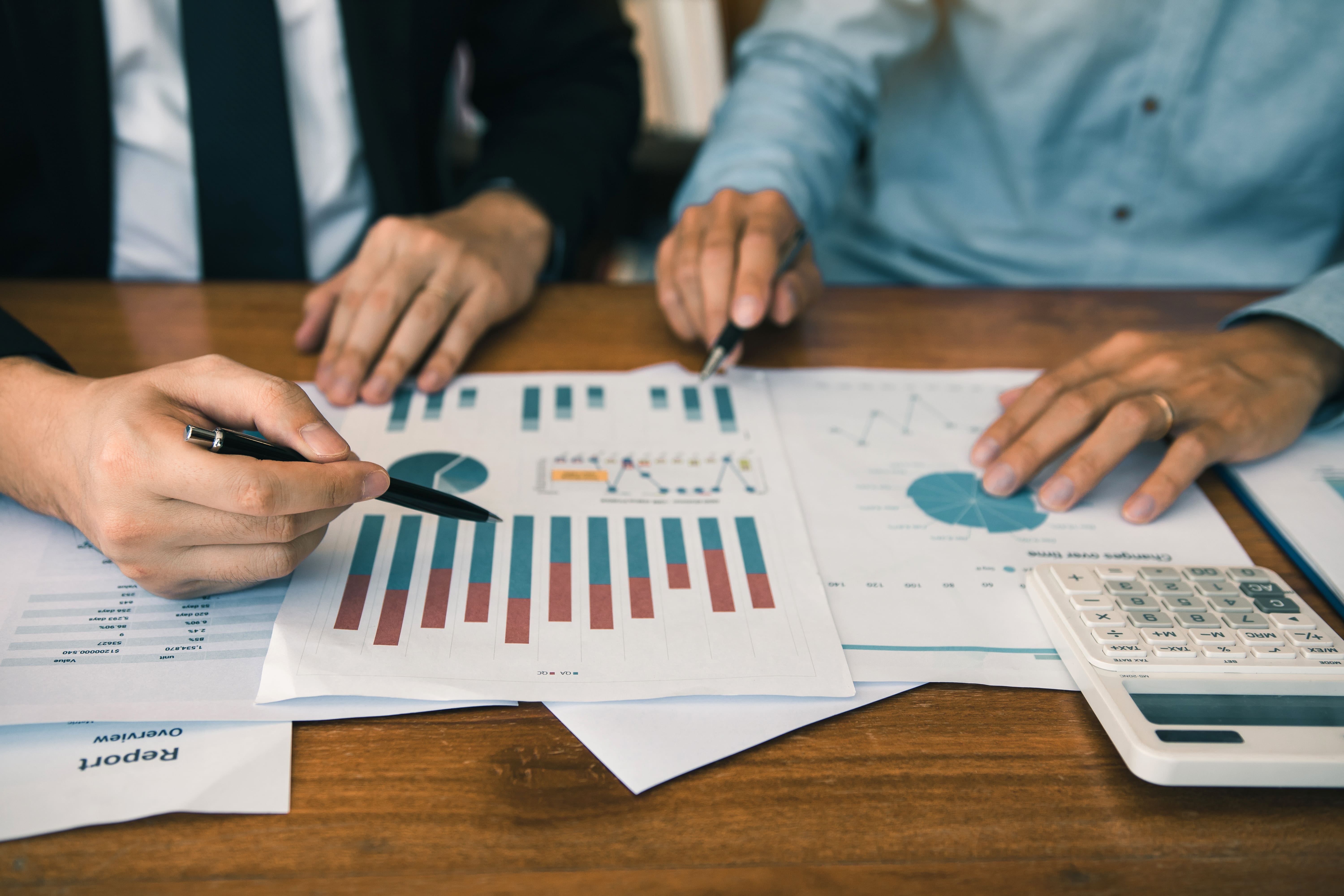
Process KPIs are indispensable for data-based process control. They provide crucial information for increasing efficiency, improving quality, controlling costs and making a company more competitive. Processes can be sustainably improved through consistent measurement, evaluation and adjustment based on defined KPIs. The decisive factor here is the selection of the KPIs relevant to the company - adapted to the industry, objectives and process structure.