What is a process map?
A process map organizes a company's business processes into clear process groups and presents them visually. This clearly shows the order in which the company processes run. The processes are summarized in three main categories:
- Core processes: These are directly related to customers and products and contribute directly to value creation.
- Management processes: They control the core processes, structure roles and tasks and are results-oriented.
- Support processes: These create the framework conditions for smooth core processes and can also be outsourced.
Why is a process landscape important?
A process map has numerous advantages for companies:
- Transparency: Employees receive a clear overview of all workflows and processes in the company.
- Bottleneck identification: Potential bottlenecks can be identified and eliminated.
- Increased efficiency: Superfluous process steps are easier to identify and eliminate.
- Standardization: Uniform workflows reduce errors and misunderstandings.
How do you create a process map?
<span class="text-highlight-purple">Um eine Prozesslandkarte zu erstellen, gibt es 2 Möglichkeiten:</span>
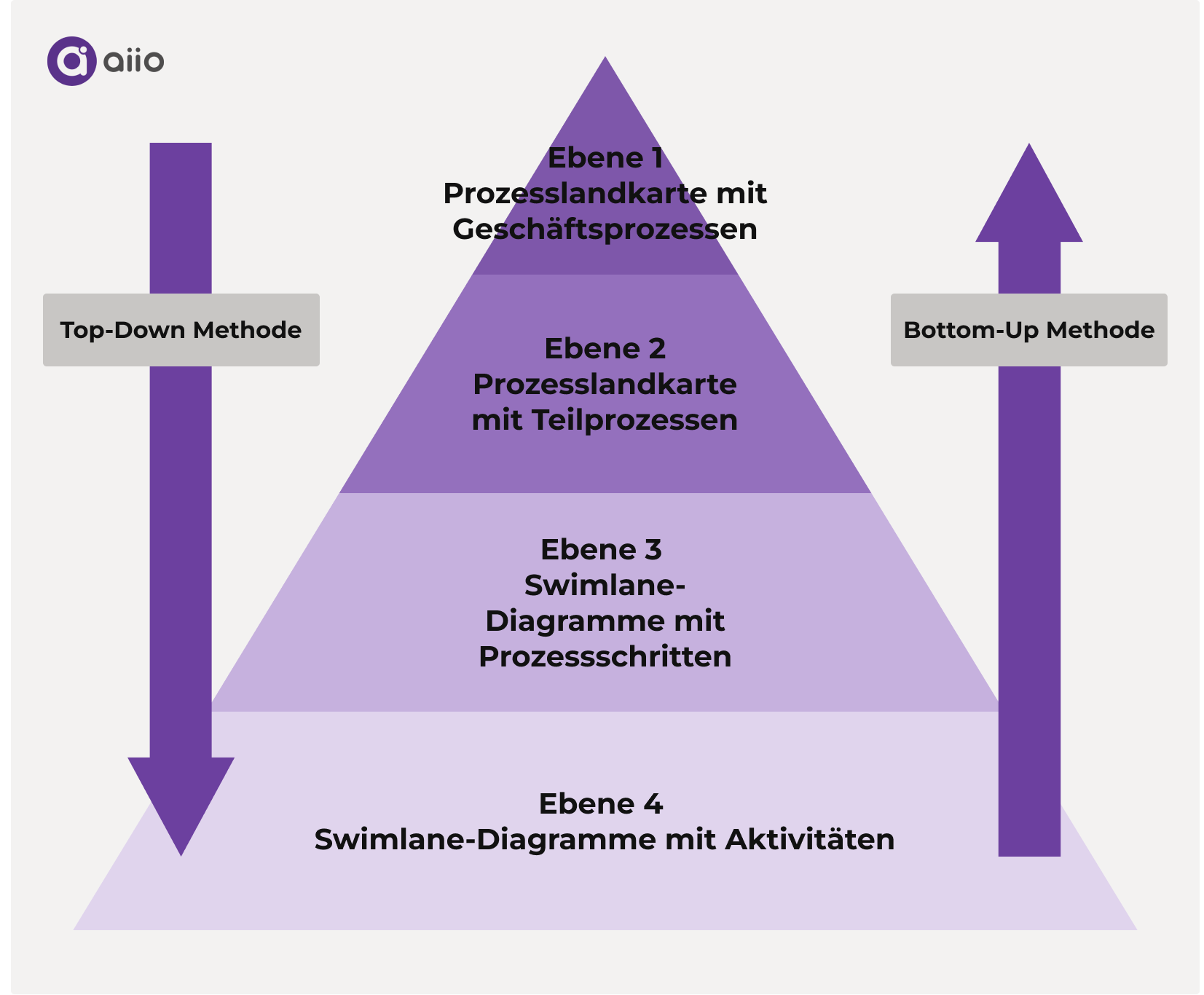
Top-down method
Here you start at management level with the process mapping, name the processes and then classify them into process types. The hierarchy levels below are added step by step.
Bottom-up method
This method maps the processes exactly as they occur in practice. The lower hierarchy levels are recorded first and the management level is included last. This approach involves all team members and promotes a good working atmosphere.
Template for process maps
A process landscape can be created using a template. We therefore offer a template that can be easily edited with PowerPoint.
Downloadable template:
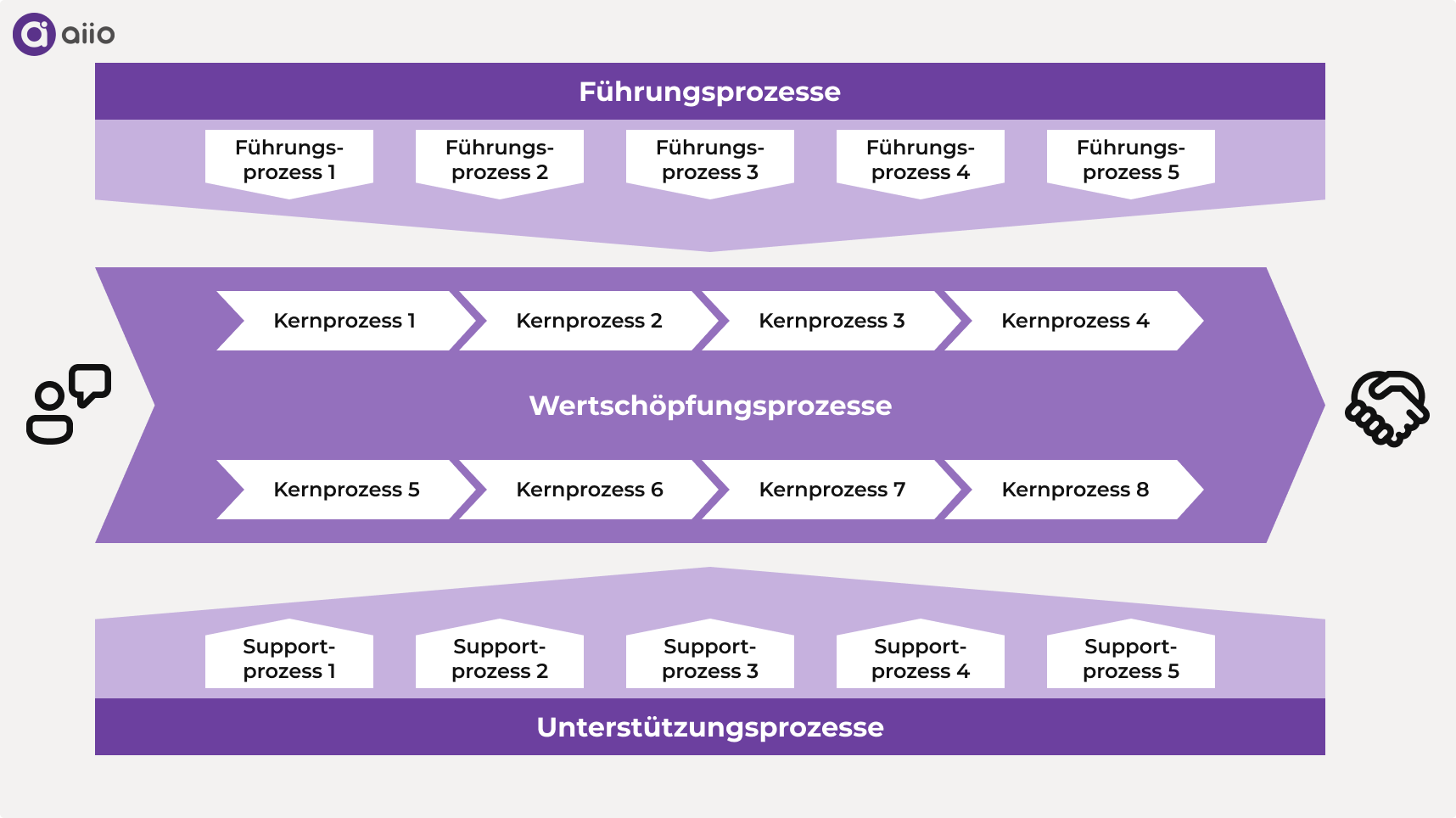
Process landscape ISO 9001
That is ISO-9001:
The ISO 9001 standard describes international standards for quality management systems. The system used in the company must demonstrably meet the requirements of customers and authorities.
It does this by:
- makes the systematic sequence of processes visible,
- presents the interactions between processes in an understandable way,
- makes it easier for auditors and employees to assess the management system.
Advantages of ISO 9001 verification:
- Increase in productivity and minimization of risks
- Higher customer satisfaction thanks to more efficient processes
- Improvement of corporate image through globally recognized certification
- Cost savings thanks to optimally designed processes
Conclusion
Process maps are a valuable tool for companies of all sizes. They create clarity about processes, make it easier to train new employees and are essential for ISO 9001 certification. With a clearly structured process map, companies can better control, optimize and make their processes transparent.